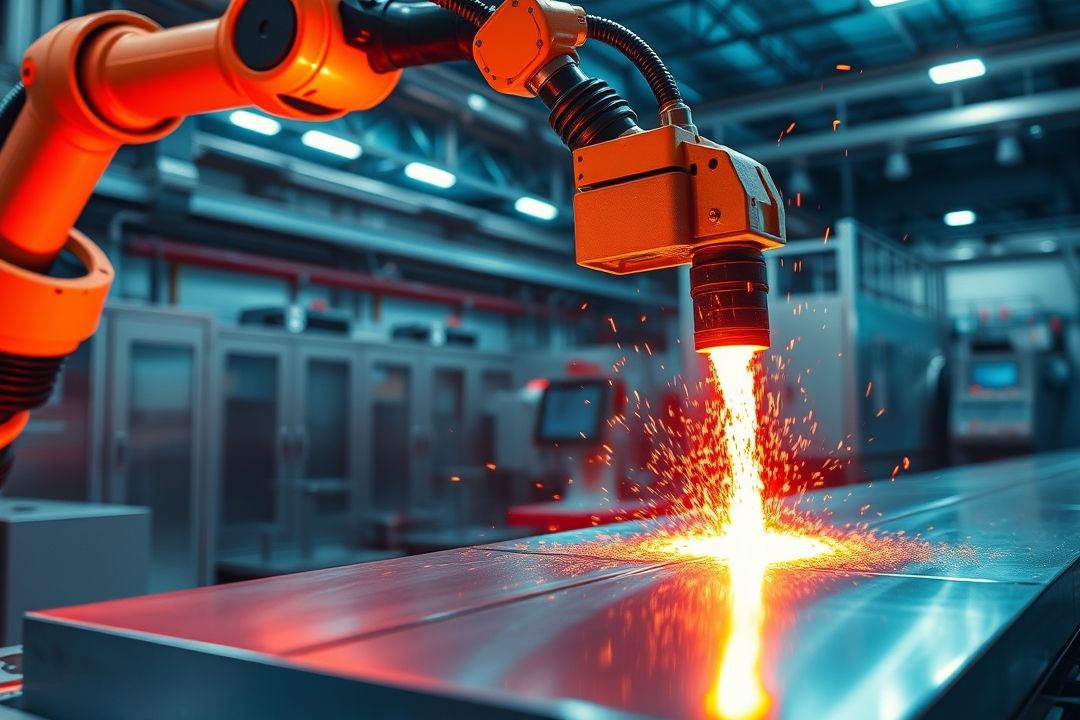
Термическое напыление: технологии, методы и применение в современной промышленности
Термическое напыление — это передовая технология, которая активно используется в различных отраслях промышленности для нанесения защитных и функциональных покрытий на поверхности изделий. Этот процесс позволяет создавать покрытия из металлов, сплавов, керамики, пластмасс и композитов, которые улучшают свойства материалов, такие как износостойкость, коррозионная стойкость, термостойкость и многое другое. В этой статье мы подробно разберем, что такое термическое напыление, как оно работает, какие методы существуют и где применяется.
Что такое термическое напыление?
Термическое напыление — это процесс, при котором материал в виде порошка или проволоки нагревается до высоких температур и распыляется на поверхность изделия. В результате на поверхности образуется тонкий слой покрытия, который может иметь толщину от 20 микрон до нескольких миллиметров. Этот метод отличается высокой скоростью нанесения и возможностью работы с большими площадями.
Для нагрева материала используются различные источники энергии, такие как электрическая дуга, плазма или пламя горения. Материал расплавляется или нагревается до полурасплавленного состояния, а затем ускоряется в направлении подложки в виде мелких частиц. При ударе о поверхность частицы сплющиваются, затвердевают и образуют плотный слой покрытия.
Преимущества термического напыления
1. Универсальность: Метод подходит для нанесения покрытий из широкого спектра материалов, включая металлы, керамику, пластмассы и композиты.
2. Толщина покрытий: Позволяет создавать как тонкие, так и толстые слои, что делает его применимым для различных задач.
3. Минимальное нагревание подложки: Поверхность изделия не подвергается значительному нагреву, что позволяет работать с термочувствительными материалами.
4. Высокая скорость нанесения: По сравнению с другими методами, такими как гальванизация или химическое осаждение, термическое напыление выполняется быстрее.
5. Экономичность: Процесс требует меньше ресурсов, чем многие традиционные методы нанесения покрытий.
Основные методы термического напыления
Существует несколько разновидностей термического напыления, каждая из которых имеет свои особенности и области применения. Рассмотрим наиболее популярные методы.
1. Газопламенное напыление
Этот метод, разработанный в начале XX века, до сих пор остается одним из самых распространенных. В процессе используется пламя, создаваемое при сгорании газа (обычно ацетилена и кислорода). Материал в виде порошка или проволоки подается в пламя, где он расплавляется и распыляется на поверхность. Скорость частиц в этом методе обычно не превышает 150 м/с, что делает его подходящим для нанесения покрытий на крупные детали.
2. Плазменное напыление
Плазменное напыление — это более современный метод, который позволяет работать с тугоплавкими материалы, такими как оксиды и молибден. В процессе используется высокотемпературная плазменная струя, температура которой может достигать 15 000 К. Материал вводится в плазменный поток, где он расплавляется и ускоряется в направлении подложки. Этот метод обеспечивает высокую плотность покрытий и часто используется в аэрокосмической и энергетической промышленности.
3. Детонационное напыление
Детонационное напыление — это уникальный метод, в котором используется взрывная волна для нагрева и ускорения частиц материала. Процесс происходит в специальной детонационной пушке, где смесь кислорода и топлива воспламеняется, создавая взрыв. Частицы материала разгоняются до сверхзвуковых скоростей и наносятся на поверхность. Этот метод позволяет создавать очень плотные и прочные покрытия с высокой адгезией.
4. Высокоскоростное кислородно-топливное напыление (HVOF)
Метод HVOF был разработан в 1980-х годах и стал популярным благодаря своей способности создавать покрытия с низкой пористостью и высокой прочностью сцепления. В процессе используется смесь кислорода и топлива, которая сгорает в камере сгорания. Образовавшийся горячий газ разгоняет частицы материала до скорости более 1000 м/с. Этот метод часто применяется для нанесения износостойких и коррозионностойких покрытий.
5. Холодное напыление
Холодное напыление — это относительно новый метод, при котором частицы материала ускоряются до высоких скоростей без значительного нагрева. Процесс происходит при комнатной температуре, что позволяет избежать окисления и деформации материала. Частицы ударяются о поверхность и образуют покрытие за счет пластической деформации. Этот метод подходит для работы с мягкими металлами, такими как медь и алюминий, а также с полимерами и композитами.
Применение термического напыления в промышленности
Термическое напыление широко используется в различных отраслях для решения множества задач. Вот несколько примеров:
1. Аэрокосмическая промышленность: Нанесение термобарьерных покрытий на лопатки турбин и другие детали, подверженные высоким температурам.
2. Энергетика: Защита компонентов электростанций от коррозии и эрозии.
3. Автомобильная промышленность: Улучшение износостойкости деталей двигателя и трансмиссии.
4. Медицина: Создание биосовместимых покрытий для медицинских имплантатов.
5. Нефтегазовая промышленность: Защита оборудования от коррозии в агрессивных средах.
Ограничения и безопасность
Несмотря на множество преимуществ, термическое напыление имеет некоторые ограничения. Например, это процесс прямой видимости, что означает невозможность нанесения покрытий на сложные или труднодоступные участки. Кроме того, механизм связи между покрытием и подложкой в основном механический, что может ограничивать прочность сцепления в некоторых случаях.
Важно также учитывать вопросы безопасности. Процесс термического напыления связан с использованием высоких температур, сжатых газов и электричества, что требует соблюдения строгих мер предосторожности. Операторы должны использовать защитное оборудование, такие как очки, респираторы и специальную одежду, чтобы избежать травм и воздействия вредных веществ.