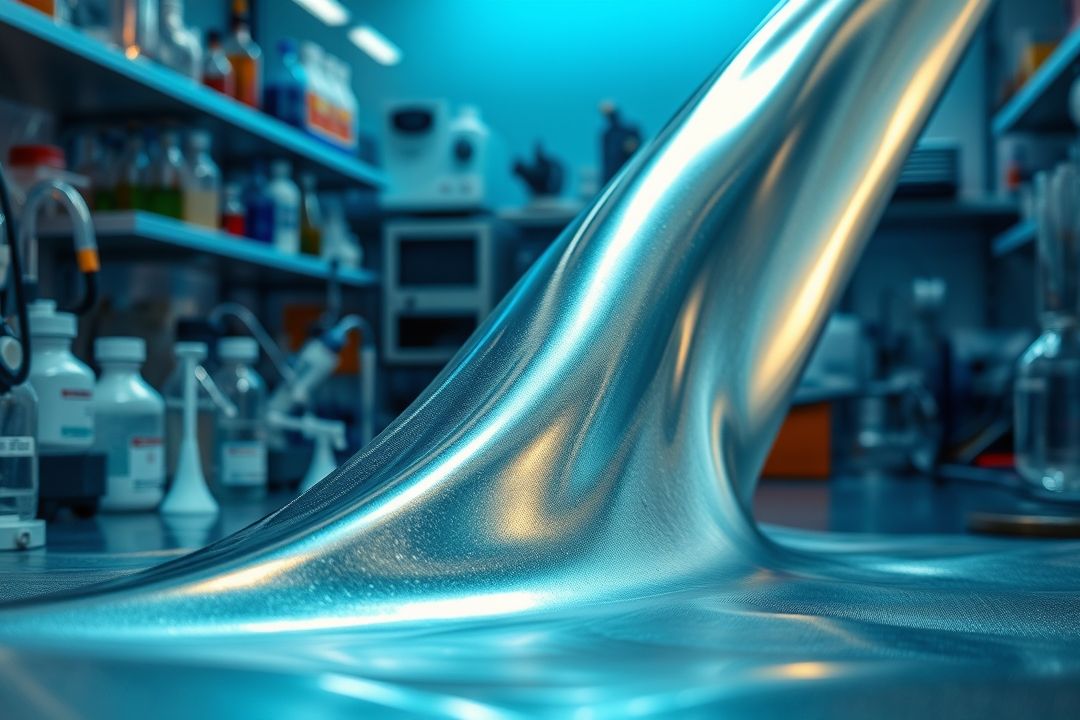
Сверхпластичность: удивительное свойство материалов, меняющее промышленность
Сверхпластичность — это уникальное свойство материалов, которое позволяет им деформироваться значительно больше, чем обычно, без разрушения. Это явление встречается в определенных металлах и керамике, которые при определенных условиях могут растягиваться в несколько раз, сохраняя свою целостность. Например, некоторые материалы могут удлиняться на 400% и более. Такие свойства делают сверхпластичность важной технологией в аэрокосмической, автомобильной и других отраслях промышленности. В этой статье мы подробно разберем, что такое сверхпластичность, как она работает и где применяется.
Что такое сверхпластичность?
Сверхпластичность — это состояние материала, при котором он может деформироваться на сотни процентов, не разрываясь. Обычно это происходит при высоких температурах, близких к половине температуры плавления материала. Например, мелкозернистые металлы и керамика демонстрируют такие свойства. Важно отметить, что сверхпластичность отличается от сверхэластичности, которая связана с восстановлением формы после деформации.
Ключевая особенность сверхпластичности — равномерное истончение материала без образования локальных сужений, которые обычно приводят к разрушению. Это происходит благодаря подавлению образования микропустот, которые обычно появляются при деформации.
История открытия сверхпластичности
Первые свидетельства сверхпластичности были обнаружены в древних артефактах, таких как сталь Вутца из древней Индии. Однако научное признание это явление получило только в XX веке. В 1912 году Бенгоу опубликовал отчет об удлинении латуни на 163%. Позже, в 1928 году, Дженкинс достиг удлинения на 300% в сплавах кадмия-цинка и свинца-олова.
Настоящий прорыв произошел в 1934 году, когда Пирсон обнаружил удлинение на 1950% в сплаве свинца и олова. Однако после этого интерес к сверхпластичности на Западе угас на несколько десятилетий. В СССР исследования продолжились, и в 1985 году в Уфе был основан Институт проблем сверхпластичности металлов — единственный в мире институт, полностью посвященный этой теме.
Современный интерес к сверхпластичности возродился в 1980-х годах, когда в Сан-Диего прошла первая международная конференция на эту тему. С тех пор сверхпластичность стала важной технологией в аэрокосмической промышленности.
Условия для сверхпластичности
Чтобы материал стал сверхпластичным, необходимо соблюдение нескольких условий. Во-первых, размер зерен должен быть очень мелким — менее 10 микрометров. Во-вторых, материал должен находиться при высокой температуре, обычно превышающей половину его абсолютной температуры плавления. Эти условия позволяют материалу деформироваться равномерно, без образования дефектов.
Важным параметром является также чувствительность к скорости деформации. Она показывает, как материал реагирует на изменения скорости деформации. Для сверхпластичных материалов этот параметр должен быть больше 0,3, а идеальное значение — 0,5.
Механизмы сверхпластичности
Основной механизм сверхпластичности — скольжение по границам зерен. Однако этот процесс может вызывать концентрацию напряжений, что приводит