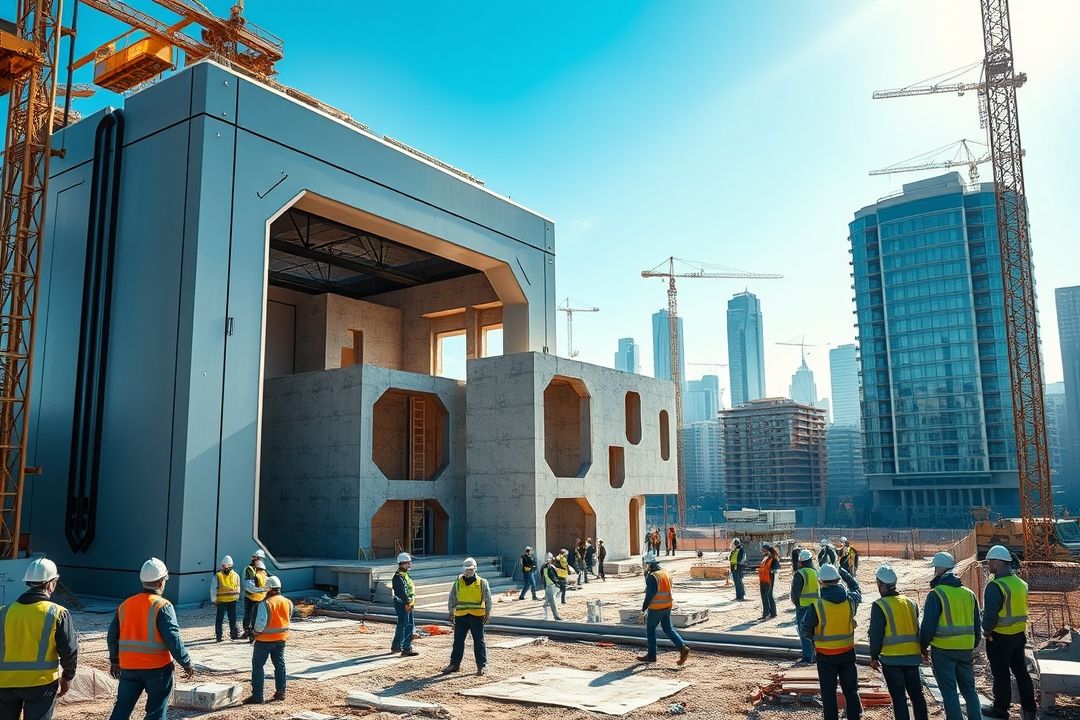
Строительная 3D-печать: революция в строительстве и производстве
Строительная 3D-печать (сокращенно c3Dp или 3DCP) — это технология, которая использует аддитивное производство для создания зданий и строительных компонентов. Этот процесс также называют аддитивным строительством. Основная идея заключается в том, чтобы слой за слоем «печатать» конструкции, используя различные материалы, такие как бетон, полимеры, глина и даже металлы. Технология уже применяется для строительства домов, мостов, инфраструктурных объектов и даже скульптур.
Как работает строительная 3D-печать?
Строительная 3D-печать использует три основных метода: экструзию, порошковую склейку и аддитивную сварку.
1. Экструзия — самый распространенный метод. Материал, например бетон или цементная смесь, подается через сопло принтера и наносится слоями. Этот метод позволяет создавать сложные формы и конструкции, которые трудно или невозможно достичь традиционными методами.
2. Порошковая склейка — здесь используется порошковый материал, который склеивается с помощью связующего вещества или спекается под воздействием высокой температуры.
3. Аддитивная сварка — применяется для работы с металлами. Металлические детали свариваются слоями, создавая прочные и долговечные конструкции.
Преимущества строительной 3D-печати
1. Скорость строительства
Технология позволяет возводить здания в разы быстрее, чем традиционные методы. Например, некоторые компании уже строят дома за 24 часа.
2. Экономия материалов
3D-печать позволяет точно контролировать количество используемого материала, минимизируя отходы.
3. Снижение затрат
Благодаря автоматизации процесса сокращаются расходы на рабочую силу и оборудование.
4. Сложные архитектурные формы
Технология открывает новые возможности для дизайна, позволяя создавать уникальные и сложные конструкции.
5. Экологическая устойчивость
3D-печать может использовать переработанные материалы, такие как пластик или строительные отходы, что делает процесс более экологичным.
История развития технологии
Строительная 3D-печать имеет долгую историю, которая начинается еще в 1939 году, когда Уильям Уршель создал первое бетонное здание, напечатанное на 3D-принтере. В 1950-х годах была концептуализирована роботизированная кирпичная кладка, а в 1960-х начались разработки автоматизированного строительства.
Одним из ключевых этапов стало изобретение метода Contour Crafting Бероком Хошневисом в 1995 году. Эта технология была разработана для экструзии керамики, но позже адаптирована для строительства. В 2000-х годах Хошневис и его команда начали экспериментировать с 3D-печатью бетона, исследуя возможности автоматизации строительного процесса.
В 2005 году итальянский инженер Энрико Дини запатентовал технологию D-Shape, которая использует струйную печать для создания крупногабаритных конструкций. Эта технология уже применялась для строительства искусственных рифов и других объектов.
Современные достижения включают строительство первого офисного здания в Дубае в 2016 году и проект Tecla в 2021 году, где был создан первый дом из глины с помощью 3D-печати.
Примеры применения
1. Жилые дома
В 2015 году в Ярославле был построен первый в Европе жилой дом с использованием 3D-печати. Стены здания были напечатаны в цеху и собраны на месте.
2. Мосты
В 2016 году в Испании был открыт первый пешеходный мост, напечатанный на 3D-принтере. Мост длиной 12 метров был создан из микрожелезобетона.
3. Офисные здания
Дубай стал пионером в области 3D-печати зданий. В 2016 году там было построено первое офисное здание площадью 250 квадратных метров.
4. Лунные базы
Технология 3D-печати рассматривается для строительства на Луне и Марсе. Европейское космическое агентство и НАСА уже разрабатывают проекты, использующие лунный реголит для печати структур.
Проблемы и вызовы
Несмотря на преимущества, строительная 3D-печать сталкивается с рядом проблем:
1. Качество материалов
Необходимо разрабатывать смеси, которые обеспечивают прочность и долговечность конструкций.
2. Стандартизация
Отрасль нуждается в единых стандартах для обеспечения безопасности и качества строительства.
3. Ограничения технологии
Текущие технологии пока не позволяют печатать здания выше нескольких этажей.
4. Стоимость оборудования
3D-принтеры для строительства пока остаются дорогостоящими, что ограничивает их доступность.
Будущее строительной 3D-печати
Технология продолжает развиваться, и в ближайшие годы мы можем ожидать значительных прорывов. Уже сейчас ведутся исследования по использованию новых материалов, таких как глина и переработанные отходы. Увеличиваются масштабы применения — от небольших домов до крупных инфраструктурных проектов.
Одним из самых перспективных направлений является строительство в труднодоступных районах. 3D-печать позволяет использовать местные материалы и сокращать логистические затраты. Это особенно важно для развития сельских регионов и зон, пострадавших от стихийных бедствий.
Экологические аспекты
Строительная 3D-печать может значительно снизить воздействие на окружающую среду. По сравнению с традиционными методы, она сокращает выбросы CO2, потребление воды и количество отходов. Например, при строительстве дома с помощью 3D-печати выбросы углекислого газа могут быть снижены на 50%.
Экономическая выгода
Технология также демонстрирует значительную экономическую эффективность. Капитальные затраты на строительство могут быть сокращены на 78%, что делает 3D-печать привлекательной для застройщиков и инвесторов.