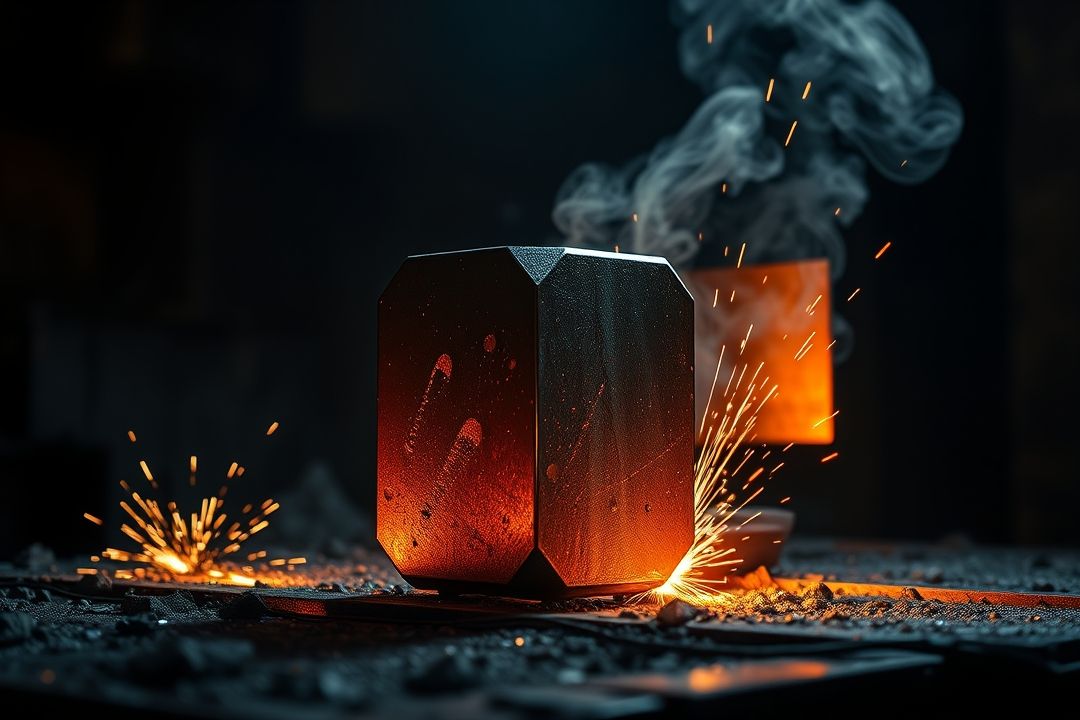
Сталь: универсальный материал, изменивший мир
Сталь — это уникальный сплав железа и углерода, который стал одним из самых важных материалов в истории человечества. Благодаря своей прочности, долговечности и относительно низкой стоимости сталь используется практически во всех сферах нашей жизни: от строительства зданий и мостов до производства автомобилей, инструментов и бытовой техники. В этой статье мы подробно рассмотрим, что такое сталь, как её производят, какие виды стали существуют и почему этот материал так важен для современной промышленности.
Что такое сталь?
Сталь — это сплав железа с углеродом, где содержание углерода обычно не превышает 2,14%. Железо является основным компонентом, но в состав стали могут добавляться и другие элементы, такие как марганец, хром, никель и молибден, чтобы придать материалу дополнительные свойства. Например, нержавеющая сталь содержит не менее 11% хрома, что делает её устойчивой к коррозии и окислению.
Сталь ценится за свою высокую прочность на разрыв, твёрдость и способность выдерживать большие нагрузки. Однако увеличение прочности часто происходит за счёт снижения пластичности. Это делает сталь идеальным материалом для конструкций, где важна устойчивость к деформациям, таких как мосты, небоскрёбы и машины.
Как производят сталь?
Производство стали — это сложный процесс, который начинается с добычи железной руды. Железо извлекается из руды путём восстановления, то есть удаления кислорода. Этот процесс называется плавкой и обычно происходит в доменных печах. После плавки получается чугун — сплав железа с высоким содержанием углерода (более 2,14%).
Чтобы превратить чугун в сталь, необходимо уменьшить содержание углерода. Это делается с помощью различных методов, таких как кислородно-конвертерный процесс (BOS) или электродуговая печь (EAF). В процессе производства также добавляются легирующие элементы, которые придают стали нужные свойства.
Современные сталелитейные заводы используют технологии непрерывной разливки, которые позволяют производить стальные слитки, слябы и прутки с минимальными потерями времени и ресурсов.
Виды стали
Существует множество видов стали, каждый из которых предназначен для определённых задач. Вот основные категории:
1. Углеродистая сталь
Самый распространённый тип, который содержит только железо и углерод. Она используется в строительстве, производстве труб и машин.
2. Нержавеющая сталь
Содержит хром и никель, что делает её устойчивой к коррозии. Используется в медицине, пищевой промышленности и производстве бытовой техники.
3. Легированная сталь
Включает дополнительные элементы, такие как марганец, хром или ванадий, для улучшения прочности, твёрдости и устойчивости к износу.
4. Инструментальная сталь