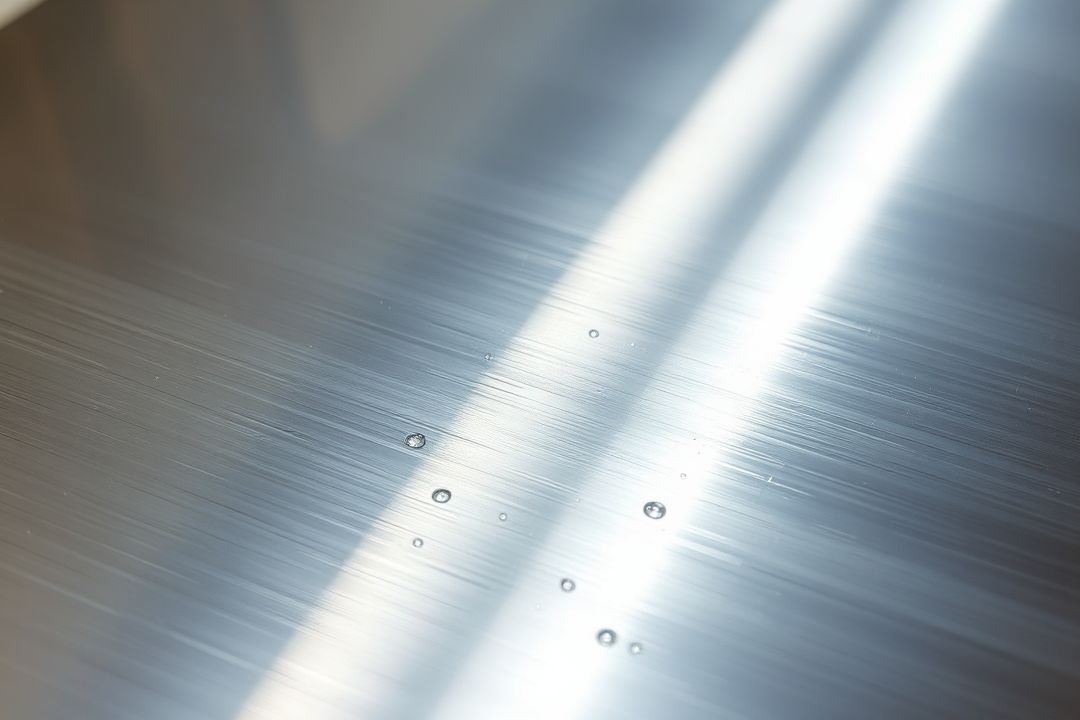
Нержавеющая сталь: Прочные и коррозионно-стойкие решения для современного мира
Нержавеющая сталь, также известная как inox или коррозионно-стойкая сталь, представляет собой сплав, который стал незаменимым материалом в различных отраслях. Этот сплав, состоящий в основном из железа и хрома, обладает уникальными свойствами, которые делают его идеальным для использования в условиях, где требуется высокая прочность и устойчивость к коррозии.
Что такое нержавеющая сталь?
Нержавеющая сталь — это сплав, который содержит не менее 10,5% хрома. Хром образует на поверхности стали тонкую защитную пленку оксида, которая предотвращает дальнейшую коррозию. В зависимости от назначения, в состав нержавеющей стали могут входить и другие элементы, такие как никель, молибден, углерод и азот. Эти добавки улучшают механические свойства и коррозионную стойкость материала.
Применение нержавеющей стали
Благодаря своим уникальным свойствам, нержавеющая сталь находит широкое применение в различных областях:
Кулинария и гастрономия
Нержавеющая сталь используется для производства кухонной посуды, столовых приборов и оборудования для ресторанов. Она легко очищается, устойчива к пятнам и не влияет на вкус пищи.
Медицина
В хирургических инструментах и медицинском оборудовании нержавеющая сталь обеспечивает высокую степень стерильности и долговечности. Она не подвержена коррозии, что делает ее идеальной для использования в операционных.
Строительство
Нержавеющая сталь используется в строительных конструкциях, таких как каркасы зданий, лестницы и перила. Она обеспечивает прочность и долговечность, а также эстетичный внешний вид.
Промышленность
В химической и нефтегазовой отраслях нержавеющая сталь используется для производства резервуаров, трубопроводов и оборудования, которое должно выдерживать агрессивные химические среды.
Транспорт
Нержавеющая сталь применяется в производстве автомобилей, судов и самолетов, где требуется высокая прочность и устойчивость к коррозии.
Характеристики нержавеющей стали
Устойчивость к коррозии
Одним из главных преимуществ нержавеющей стали является ее высокая устойчивость к коррозии. Хотя нержавеющая сталь может ржаветь, это происходит только на поверхности, в то время как внутренние слои остаются защищенными. Хром, содержащийся в сплаве, образует защитную пленку, которая восстанавливается даже при повреждении.
Прочность
Нержавеющая сталь обладает высокой прочностью и может выдерживать значительные нагрузки. Например, сталь марки 304 имеет предел текучести около 210 МПа, а с помощью холодной обработки ее прочность можно увеличить до 1 050 МПа. Это делает нержавеющую сталь идеальным материалом для конструкций, требующих высокой прочности.
Температура плавления
Температура плавления нержавеющей стали варьируется от 1400 до 1530 °C, что значительно выше, чем у алюминия или меди. Это позволяет использовать нержавеющую сталь в условиях высоких температур.
Проводимость
Нержавеющая сталь является относительно плохим проводником электричества. Это делает ее менее подходящей для применения в электрических соединениях, однако в некоторых случаях, где требуется коррозионная стойкость, нержавеющая сталь может быть использована.
Магнетизм
Некоторые виды нержавеющей стали, такие как мартенситные и ферритные, обладают магнитными свойствами, в то время как аустенитные стали обычно немагнитны. Это свойство может быть важным при выборе материала для определенных приложений.
История нержавеющей стали
История нержавеющей стали начинается с конца 18 века, когда ученые начали исследовать свойства хрома. В 1821 году Пьер Бертье впервые