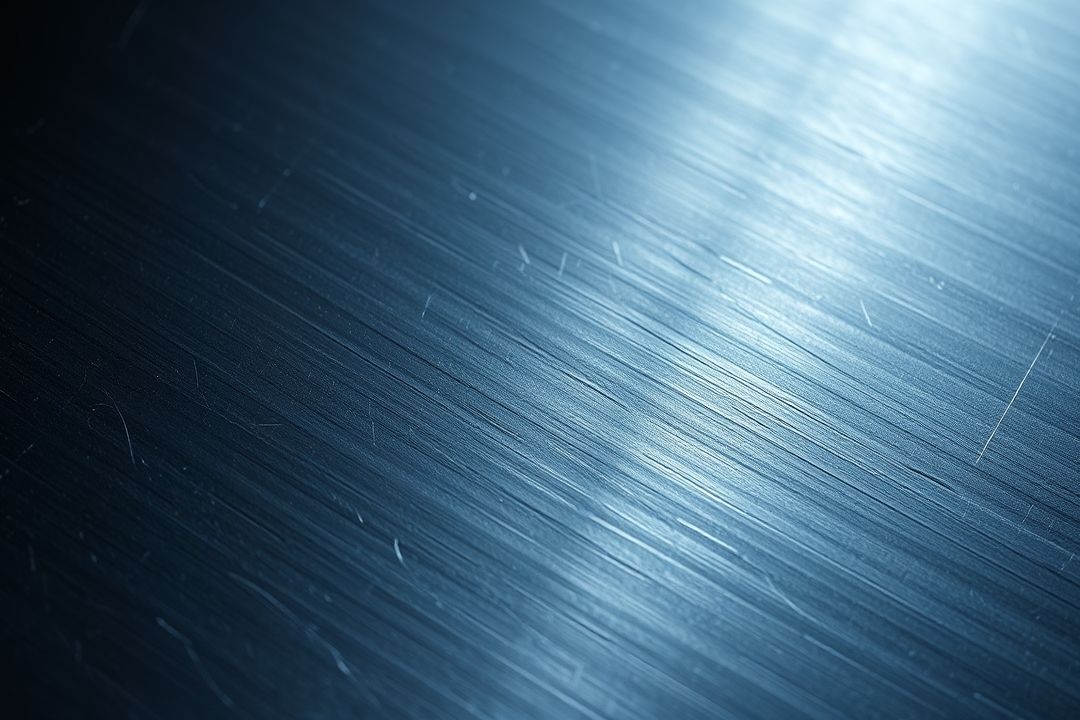
Мартенситная нержавеющая сталь: особенности, история и применение
Мартенситная нержавеющая сталь — это уникальный тип сплава, который отличается своей мартенситной кристаллической структурой. Этот материал можно закаливать и подвергать термической обработке, что позволяет ему приобретать различные механические свойства. В мире нержавеющей стали существуют и другие типы, такие как аустенитная, ферритная, дуплексная и дисперсионно-закаленная, но мартенситная сталь занимает особое место благодаря своим характеристикам.
История мартенситной нержавеющей стали
История мартенситной нержавеющей стали начинается в начале XX века. В 1912 году Гарри Брирли, работая в исследовательской лаборатории Браун-Фирта в Шеффилде, Англия, искал коррозионно-стойкий сплав для оружейных стволов. В результате его исследований был открыт мартенситный сплав нержавеющей стали, который вскоре стал популярным в промышленности. Открытие Брирли было опубликовано в газете *The New York Times* в январе 1915 года, а сам сплав был запатентован в том же году.
Сплав, который позже стал известен под брендом «Staybrite», использовался в различных конструкциях, включая навес над входом в знаменитый отель Savoy в Лондоне в 1929 году. Интересно, что характерная тетрагональная мартенситная микроструктура была впервые описана немецким микроскопистом Адольфом Мартенсом в конце XIX века. В 1912 году Элвуд Хейнс также подал заявку на патент на мартенситный сплав, который был выдан только в 1919 году.
Обзор мартенситной нержавеющей стали
Мартенситные нержавеющие стали могут быть как высоко-, так и низкоуглеродистыми. Они изготавливаются на основе железа с содержанием хрома от 12% до 17% и углерода от 0,10% (тип 410) до 1,2% (тип 440C). Некоторые марки, такие как тип 431, могут содержать никель, что позволяет улучшить коррозионную стойкость и повысить прочность за счет снижения содержания углерода.
Например, марка EN 1.4313 (CA6NM) с низким содержанием углерода, 13% хрома и 4% никеля, обладает хорошими механическими свойствами и свариваемостью. Она используется в гидроэлектростанциях по всему миру, включая знаменитую плотину «Три ущелья» в Китае. Добавление таких элементов, как бор, кобальт, ниобий и титан, улучшает высокотемпературные свойства стали, что делает ее идеальной для использования в теплообменниках паровых турбин.
Специальная марка, известная как тип 630 (или 17-4 PH), представляет собой мартенситную сталь, которая затвердевает при осаждении при температуре 475 °C (887 °F). Это делает ее особенно ценной в различных промышленных приложениях.
Химический состав мартенситной нержавеющей стали
Химический состав мартенситной нержавеющей стали варьируется в зависимости от типа и назначения. Например, в стали типа 410 содержание углерода может достигать 0,45%, что обеспечивает высокую прочность. Важно отметить, что существует множество фирменных марок, которые не всегда указаны в стандартах, особенно в производстве столовых приборы.
Механические свойства
Мартенситные нержавеющие стали закаливаются с помощью термической обработки, что включает в себя закалку и отпуск. Процесс закалки приводит к образованию мартенсита, который обладает высокой твердостью и прочностью. Однако незакаленный мартенсит имеет низкую вязкость и может быть хрупким. Закаленный мартенсит, напротив, обеспечивает хорошую твердость и высокую вязкость, что делает его идеальным для использования в медицинских инструментах, таких как скальпели и бритвы.
При термической обработке обозначение QT означает закалку и отпуск, а P — дисперсионное твердение. Эти процессы позволяют достичь оптимальных механических свойств, необходимых для различных применений.
Физические свойства
Физ).