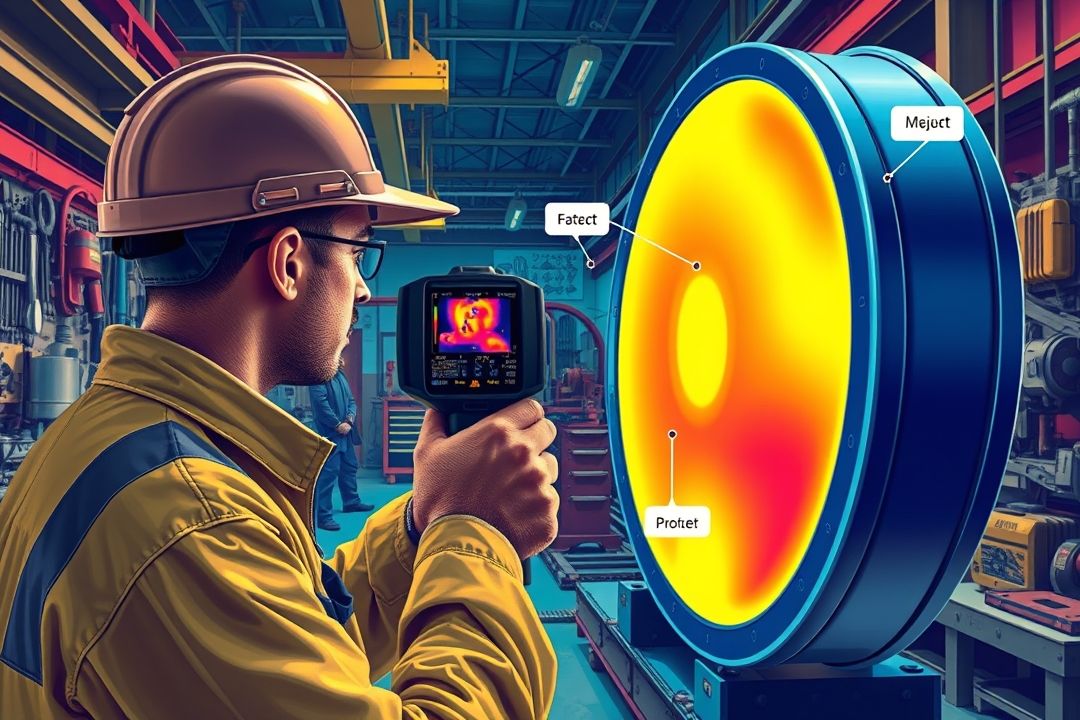
Инфракрасный неразрушающий контроль материалов: современный подход к качеству и безопасности
В современной промышленности и производстве контроль качества материалов играет ключевую роль. Одним из самых эффективных методов, который завоевал популярность благодаря своей точности и универсальности, является инфракрасный неразрушающий контроль (IRNDT). Этот метод позволяет выявлять дефекты в материалах без их повреждения, что делает его незаменимым в различных отраслях.
Что такое инфракрасный неразрушающий контроль?
Инфракрасный неразрушающий контроль (IRNDT) — это технология, основанная на использовании теплового излучения для анализа состояния материалов. Суть метода заключается в том, что материал подвергается внешнему воздействию, например, нагреву, а затем с помощью инфракрасной камеры фиксируется его тепловой отклик. Это позволяет обнаружить дефекты, такие как трещины, пустоты, раковины и другие неоднородности, которые могут быть скрыты под поверхностью.
Как работает IRNDT?
Процесс IRNDT начинается с возбуждения материала внешним источником энергии. В качестве таких источников могут использоваться галогенные лампы, импульсные лампы, ультразвуковые устройства или даже лазеры. Когда материал нагревается, его поверхность начинает излучать тепло. Инфракрасная камера фиксирует это излучение и создает термограмму — изображение, которое показывает распределение температуры на поверхности материала.
Если в материале есть дефекты, они нарушают равномерность теплового потока, что приводит к появлению температурных аномалий на термограмме. Например, трещина или пустота может вызвать локальное повышение или понижение температуры, что сразу становится заметным при анализе данных.
Преимущества инфракрасного неразрушающего контроля
1. Бесконтактность
Метод IRNDT не требует прямого контакта с материалом, что исключает риск его повреждения. Это особенно важно при работе с хрупкими или дорогостоящими материалами.
2. Высокая скорость
Современные инфракрасные камеры позволяют проводить измерения за считанные секунды, что делает метод идеальным для массового контроля на производственных линиях.
3. Универсальность
IRNDT подходит для анализа широкого спектра материалов, включая металлы, пластики, композиты и даже керамику.
4. Безопасность
Поскольку метод не использует вредных излучений, таких как рентгеновские лучи, он безопасен для операторов и окружающей среды.
Введение в инфракрасную термографию
Инфракрасная термография — это технология, лежащая в основе IRNDT. Она основана на том, что все объекты, температура которых выше абсолютного нуля, излучают тепло в инфракрасном диапазоне. Инфракрасная камера улавливает это излучение и преобразует его в видимое изображение, где разные цвета соответствуют разным температурам.
Одним из ключевых преимуществ термографии является ее способность измерять температуру на больших площадях. Это позволяет анализировать не только отдельные точки, но и целые объекты, что особенно полезно в промышленных условиях.
Однако важно помнить, что на точ