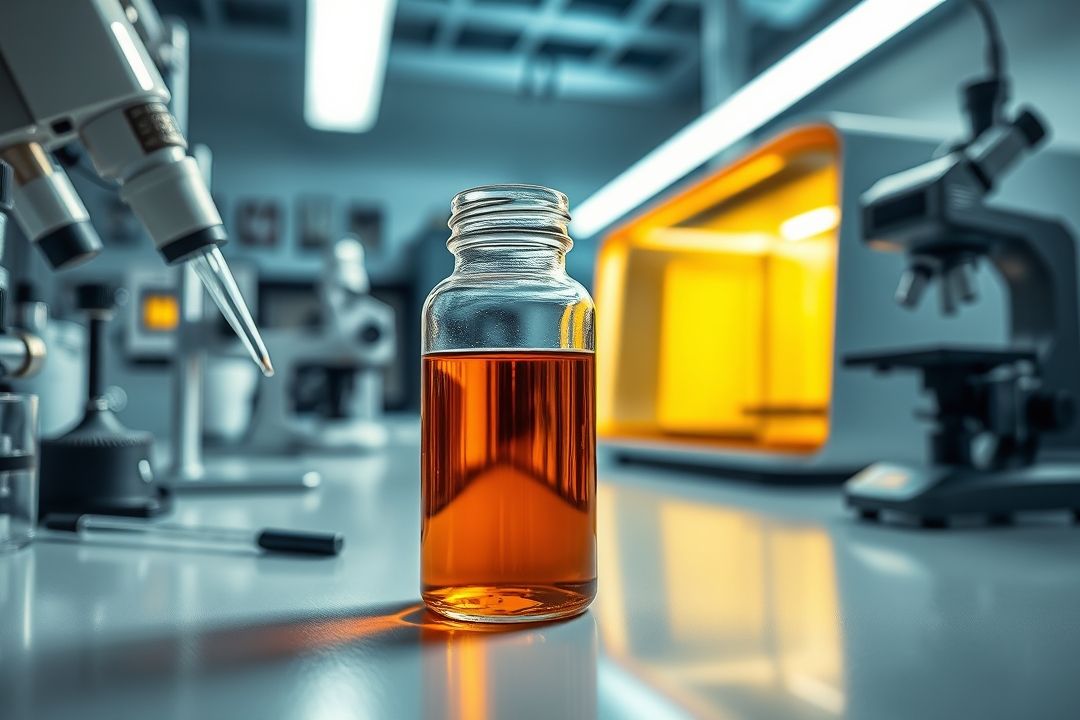
SU-8: Негативный фоторезист для микроэлектроники и микрофлюидики
SU-8 — это популярный негативный фоторезист, который широко используется в микроэлектронной промышленности и других областях, связанных с производством микро- и наноразмерных структур. Этот материал основан на эпоксидной смоле и обладает уникальными свойствами, которые делают его идеальным для создания высокоточных шаблонов и деталей.
Что такое негативный фоторезист?
Негативный фоторезист — это тип фоточувствительного материала, который изменяет свои свойства под воздействием ультрафиолетового (УФ) излучения. В случае SU-8, участки, которые подвергаются облучению, сшиваются, что делает их нерастворимыми в процессе проявления. Остальная часть пленки остается растворимой и может быть легко удалена, что позволяет создавать сложные структуры с высоким разрешением.
Структура и состав SU-8
Название SU-8 происходит от наличия восьми эпоксидных групп в его молекуле. Эти эпоксидные группы играют ключевую роль в процессе полимеризации, который происходит при облучении. SU-8 может быть использован для создания пленок различной толщины — от менее 1 микрометра до более 300 микрометров. Также доступны сухие пленки толщиной до 1 миллиметра, которые могут быть использованы для ламинирования.
Одной из особенностей SU-8 является его способность создавать структуры с высоким соотношением сторон. Это означает, что можно получать детали с вертикальными стенками и сложными геометрическими формами. Например, соотношение сторон более 20 было достигнуто при использовании раствора, а более 40 — при использовании сухого резиста.
Оптимальные условия для работы с SU-8
SU-8 обладает максимальным поглощением в УФ-диапазоне с длиной волны 365 нм. Это делает его идеальным для использования в литографии, где требуется высокая точность. При облучении длинные молекулы SU-8 сшиваются, что приводит к полимеризации материала. В качестве растворителей в SU-8 используются гамма-бутиролактон или циклопентанон, в зависимости от конкретного состава.
История и применение SU-8
SU-8 был разработан для микроэлектронной промышленности с целью создания высококачественных масок для производства полупроводниковых приборов. Однако со временем его применение расширилось, и сегодня он активно используется в микрофлюидики, микроэлектромеханических системах (МЭМС) и в биомедицинских приложениях.
Одним из основных направлений использования SU-8 является мягкая литография, которая позволяет создавать сложные микроструктуры. Этот метод особенно полезен в области биомедицинских исследований, где требуется высокая точность и биосовместимость материалов.
Состав и обработка SU-8
SU-8 состоит из новолачной эпоксидной смолы с бисфенолом А, растворенной в органическом растворителе. В состав также могут входить соли триарилсульфония или гексафторантимоната, которые служат генераторами фотокислоты. Эти компоненты обеспечивают фоточувствительность и позволяют контролировать процесс полимеризации.
Обработка SU-8 требует особого внимания к температурным условиям на различных этапах. Время выпечки зависит от толщины слоя: чем толще слой, тем дольше он должен подвергаться обжигу. Мягкая выпечка — это ключевой этап, который позволяет удалить растворитель и сделать слой твердым. Обычно после этого этапа остается около 5% растворителя, и чем толще покрытие, тем сложнее его удалить.
Процесс обжига включает два этапа: сначала слой выдерживается при температуре 65 °C, затем температура повышается до 95 °C. Это позволяет избежать образования трещин и других дефектов, которые могут возникнуть из-за испарения растворителя.
После обжига слой SU-8 можно обнажить с помощью фотомаски с инверсным рисунком. В время экспонирования зависит от толщины пленки и дозы воздействия. После этого необходимо провести дополнительный обжиг для завершения полимеризации, что делает структуру более устойчивой к химическим воздействиям и радиации.
Новые составы SU-8
Существуют различные модификации SU-8, которые предназначены для специфических приложений. Например, в серии SU-8 2000 используется циклопентанон в качестве основного растворителя, что позволяет создавать пленки толщиной от 1 микрометра до нескольких сотен микрометров.