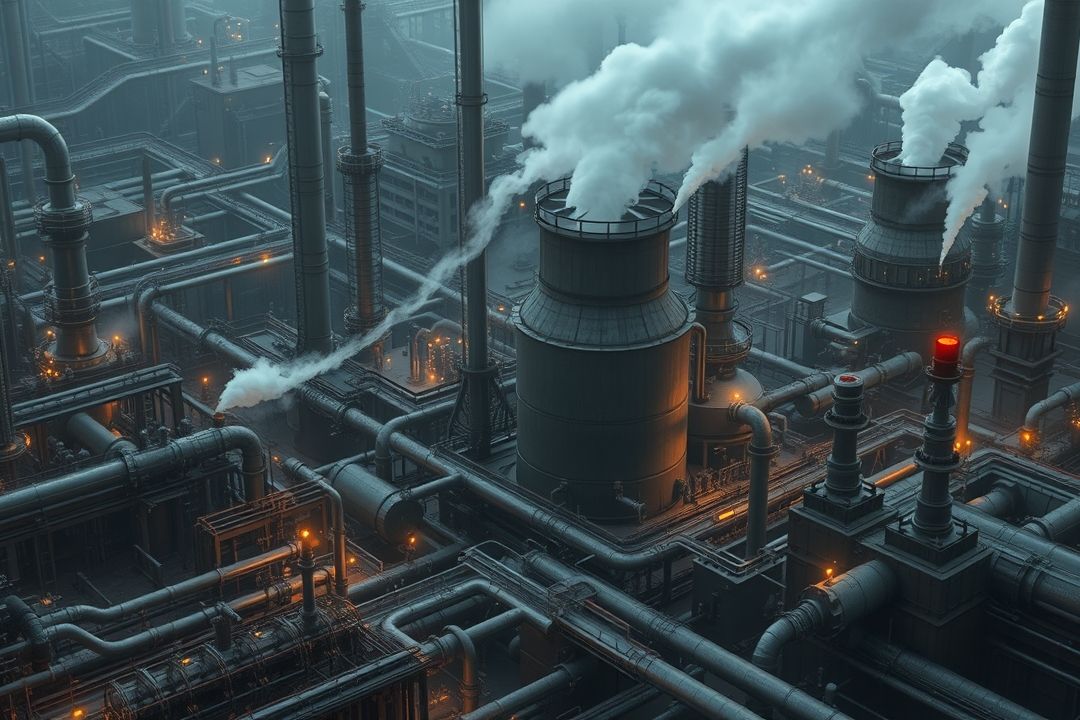
Что такое замедленное коксование? Процесс, который превращает отходы в топливо
Замедленное коксование — это один из ключевых процессов в нефтепереработке, который позволяет превращать остаточные продукты переработки нефти в полезное топливо. Этот метод не только помогает эффективно использовать ресурсы, но и снижает количество отходов, которые могут нанести вред окружающей среде. В этой статье мы подробно разберем, что такое замедленное коксование, как оно работает, и почему оно так важно для современной промышленности.
История замедленного коксования
Процесс замедленного коксования имеет долгую историю, которая началась в конце XIX века. В 1891 году русский инженер Владимир Шухов запатентовал технологию термического крекинга, которая легла в основу современных методов переработки нефти. Его изобретение позволило превращать тяжелые фракции нефти в более легкие и полезные продукты, такие как бензин и дизельное топливо.
Однако настоящий прорыв произошел в 1913 году, когда американские инженеры Уильям Бертон и Роберт Хамфри усовершенствовали процесс, разработав так называемый «процесс Бертона». Этот метод позволил удвоить количество бензина, которое можно было получить из сырой нефти. С тех пор замедленное коксование стало неотъемлемой частью нефтеперерабатывающей промышленности.
Как работает замедленное коксование?
Замедленное коксование — это процесс термического крекинга, который происходит при высоких температурах и давлении. Основная цель этого процесса — разложение тяжелых углеводородных цепочек на более мелкие и полезные молекулы. Давайте разберем этапы этого процесса подробнее.
Подготовка сырья
В качестве сырья для замедленного коксования используются остаточные продукты нефтепереработки, такие как мазут или гудрон. Эти материалы считаются отходами, так как их сложно использовать в других процессах. Однако благодаря замедленному коксованию они превращаются в ценные продукты.
Нагрев и крекинг
Сырье нагревается до температуры от 415° до 450° по Цельсию (779° до 842° по Фаренгейту) в специальных барабанах. Под воздействием высокой температуры сложные молекулы углеводородов распадаются на более простые. Этот процесс называется термическим крекингом.
Образование кокса
В результате крекинга образуются не только легкие фракции, такие как бензин и нафта, но и твердый остаток — нефтяной кокс. Этот продукт состоит в основном из углерода и может использоваться в качестве топлива или сырья для других промышленных процессов.
Разделение продуктов
После завершения процесса продукты разделяются на жидкие, газообразные и твердые фракции. Жидкие и газообразные продукты, такие как бензин, дизельное топливо и сжиженный нефтяной газ (СНГ), отправляются на дальнейшую переработку или используются в качестве топлива. Нефтяной кокс может быть использован в угольных печах, но требует дополнительной очистки из-за высокого содержания тяжелых металлов и серы.
Преимущества замедленного коксования
Замедленное коксование имеет несколько ключевых преимуществ, которые делают его важным процессом в нефтепереработке:
Эффективное использование ресурсов
Этот процесс позволяет превращать отходы нефтепереработки в ценные продукты, такие как бензин, дизельное топливо и сжиженный нефтяной газ. Это снижает количество отходов и повышает эффективность использования сырья.
Гибкость в выборе сырья
Установки замедленного коксования могут работать с различными видами сырья, включая мазут, гудрон и даже отработанные нефтяные шламы. Это делает процесс универсальным и применимым в разных условиях.
Производство нефтяного кокса
Нефтяной кокс, который образуется в процессе, может использоваться в качестве топлива или сырья для производства электродов и других материалов. Однако его использование требует осторожности из-за высокого содержания загрязняющих веществ.
Снижение экологического воздействия
Благодаря замедленному коксованию уменьшается количество отходов, которые необходимо утилизировать. Это снижает нагрузку на окружающую среду и уменьшает риски загрязнения воды и почвы.
Недостатки и экологические аспекты
Несмотря на свои преимущества, замедленное коксование имеет и некоторые недостатки, особенно в экологическом плане. Основная проблема связана с образованием нефтяного кокса, который содержит тяжелые металлы и серу. При сжигании кокса в атмосферу могут выделяться опасные вещества, такие как свинец и ртуть. Поэтому перед использованием нефтяного кокса в качестве топлива его необходимо очистить.
Кроме того, сам процесс замедленного коксования требует значительных энергозатрат и может быть источником выбросов парниковых газов. Однако современные технологии позволяют минимизировать эти воздействия за счет использования систем очистки и утилизации отходов.
Сравнение с другими процессами
Замедленное коксование — не единственный метод переработки тяжелых фракций нефти. Существуют и другие процессы, такие как жидкое коксование и гибкое коксование, которые также используются в промышленности. Однако каждый из этих методов имеет свои особенности.
Например, жидкое коксование ориентировано на производство сжиженного нефтяного газа (СНГ) и топлива для реактивных двигателей. Гибкое коксование, в свою очередь, позволяет регулировать выход продуктов в зависимости от потребностей производства. Однако замедленное коксование остается наиболее распространенным методом благодаря своей универсальности и эффективности.
Еще один процесс, который стоит упомянуть, — это висбрекинг. В отличие от замедленного коксования, висбрекинг является некаталитическим процессом, который не предполагает химических реакций. Он считается более чистым методом, так как производит меньше побочных продуктов. Однако висбрекинг пока не получил широкого распространения в промышленности.
Применение продуктов замедленного коксования
Продукты, полученные в результате замедленного коксования, находят широкое применение в различных отраслях промышленности. Давайте рассмотрим основные из них:
Бензин и дизельное топливо
Эти продукты используются в качестве топлива для автомобилей, грузовиков и другой техники. Они являются основными источниками энергии в транспортной отрасли.
Сжиженный нефтяной газ (СНГ)
СНГ используется для отопления, приготовления пищи и в качестве топлива для автомобилей. Он также применяется в химиной промышленности для производства пластмасс и других материалов.
Нефтяный кокс
Нефтяной кокс используется в качестве топлива в угольных печах, а также в производстве электродов для алюминиевой промышленности. Однако его использование требует осторожности из-за высокого содержания загрязняющих веществ.
Нафта
Нафта используется в качестве сырья для производства бензина, а также в химической промышленности для производства пластмасс и других материалов.
Будущее замедленного коксования
С развитием технологий и ужесточением экологических норм процесс замедленного коксования продолжает совершенствоваться. Современные установки оснащаются системами очистки и утилизации отходов, что позволяет снизить их воздействие на окружающую среду. Кроме того, ведутся исследования по разработке новых методов переработки тяжелых фракций нефти, которые могут стать альтернативой замедленному коксованию.
Однако пока этот процесс остается одним из наиболее эффективных способов переработки остаточных продуктов нефтепереработки. Благодаря своей универсальности и способности превращать отходы в ценные продукты, замедленное коксование продолжает играть важную роль в нефтеперерабатывающей промышленности.