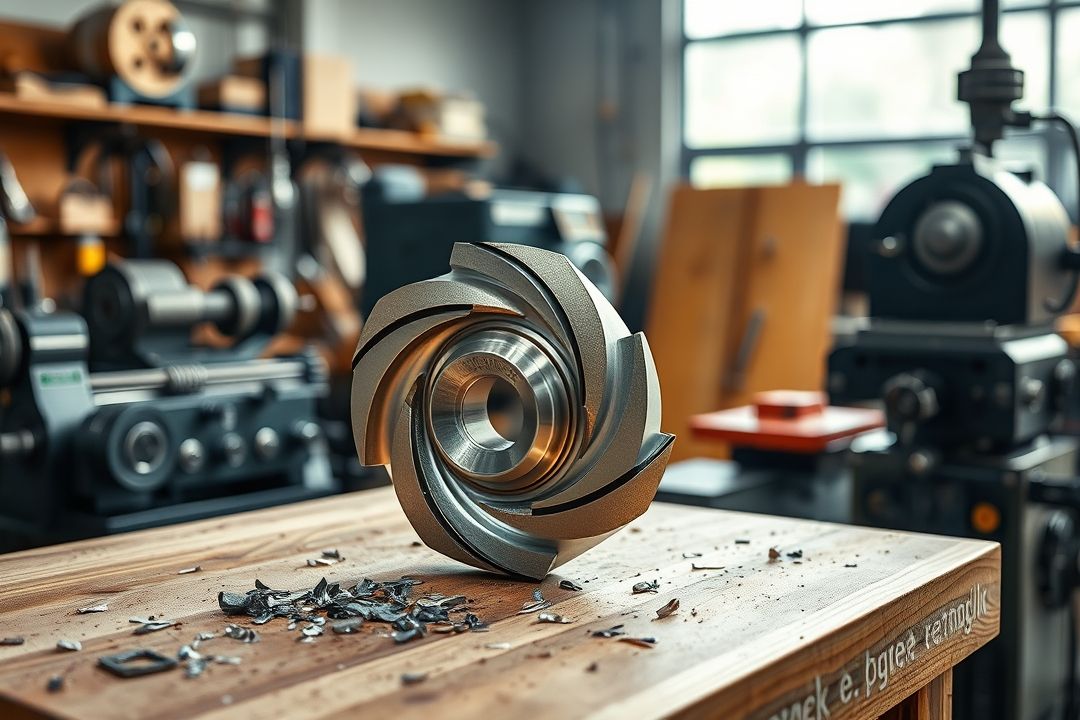
Что такое твердосплавный инструмент? Полное руководство для начинающих и профессионалов
Твердосплавный инструмент — это незаменимый элемент в современной промышленности, производстве и механике. Если вы когда-либо работали с металлом, деревом или другими материалами, то наверняка сталкивались с инструментами, оснащёнными твердосплавными наконечниками или лезвиями. Но что же такое твердосплавный инструмент, и почему он так популярен? Давайте разберёмся.
Что такое твердосплавный инструмент?
Твердосплавный инструмент — это любой инструмент, рабочая поверхность или наконечник которого изготовлены из карбида. Карбид — это материал, который получают путём соединения углерода с другими элементами, такими как вольфрам, кремний или титан. Этот материал обладает исключительной твёрдостью и износостойкостью, что делает его идеальным для режущих и обрабатывающих инструментов.
Твердосплавные инструменты используются в самых разных сферах: от ручных инструментов, таких как отвертки и пилы, до крупного промышленного оборудования, включая фрезерные станки, токарные станки и оборудование для резки металла. Например, большинство современных сверл оснащены твердосплавными наконечниками, а пилы для деревообработки — твердосплавными зубьями.
Как изготавливают твердосплавные инструменты?
Интересно, что твердосплавные инструменты редко изготавливаются полностью из карбида. Вместо этого их основу составляет сталь или другой недорогой металл, а твердосплавный наконечник или лезвие прикрепляются к этой основе с помощью специальных технологий, таких как пайка. Например, пильный диск с твердосплавными зубьями изготавливается из стали, а режущие элементы из карбида крепятся к его краям.
Почему так? Карбид, несмотря на свою твёрдость, является хрупким материалом. Использование стали в качестве основы повышает прочность и долговечность инструмента, а также снижает его стоимость. Карбид — дорогой материал, и его использование только для режущих поверхностей делает инструменты более доступными для потребителей.
Преимущества твердосплавных инструментов
Твердосплавные инструменты обладают рядом преимуществ по сравнению с традиционными стальными или композитными инструментами. Вот основные из них:
Высокая износостойкость
Карбид изнашивается гораздо медленнее, чем сталь, что делает инструменты более долговечными.
Термостойкость
Твердосплавные инструменты способны выдерживать высокие температуры без повреждений, что позволяет использовать их в интенсивных производственных процессах.
Чистота реза
Благодаря своей твёрдости, карбид обеспечивает точные и чистые разрезы, что улучшает качество готовой продукции.
Долгий срок службы
Твердосплавные инструменты служат дольше, что снижает затраты на техническое обслуживание и увеличивает производительность.
Где применяются твердосплавные инструменты?
Твердосплавные инструменты нашли широкое применение в различных отраслях. Вот несколько примеров:
Металлообработка
Твердосплавные фрезы, резцы и сверла используются для обработка металлов, включая сталь, алюминий и титан.
Деревообработка
Пилы, фрезы и строгальные ножи с твердосплавными лезвиями обеспечивают точную и чистую обработку древесины.
Строительство
Твердосплавные буры и коронки используются для сверления бетона, кирпича и других твёрдых материалов.
Производство
Твердосплавные инструменты применяются в станках для резки, шлифовки и обработки различных материалов.
Как затачивать твердосплавные инструменты?
Одним из ключевых преимуществ твердосплавных инструментов является возможность их заточки. Однако из-за высокой твёрдости карбида этот процесс требует использования специальных материалов. Для заточки твердосплавных инструментов обычно применяют алмазные или твердосплавные круги. Хотя такие круги дороги, они позволяют продлить срок службы инструмента и восстановить его рабочие характеристики.
Затачивать твердосплавные инструменты можно многократно, пока их режущая поверхность не износится полностью. Это делает их экономически выгодными в долгосрочной перспективе.
Почему твердосплавные инструменты так популярны?
Популярность твердосплавных инструментов объясняется их уникальными свойствами. Они сочетают в себе высокую твёрдость, износостойкость и термостойкость, что делает их незаменимыми в условиях интенсивной эксплуатации. Кроме того, их долговечность и возможность заточки снижают затраты на замену и техническое обслуживание.
Как выбрать твердосплавный инструмент?
При выборе твердосплавного инструмента важно учитывать несколько факторов:
Тип работы
Для разных задач подходят разные инструменты. Например, для обработки металла нужны фрезы и резцы, а для деревообработки — пилы и строгальные ножи.
Качество карбида
Обратите внимание на марку карбида и его состав. Вольфрамовый карбид считается одним из самых прочных и износостойких.
Производитель
Выбирайте инструменты от проверенных производителей, которые гарантируют качество и долговечность.
Стоимость
Твердосплавные инструменты дороже стальных, но их долговечность и производительность оправдывают вложения.
Будущее твердосплавных инструментов
С развитием технологий твердосплавные инструменты продолжают совершенствоваться. Учёные и инженеры работают над созданием новых сплавов, которые будут ещё более прочными, из