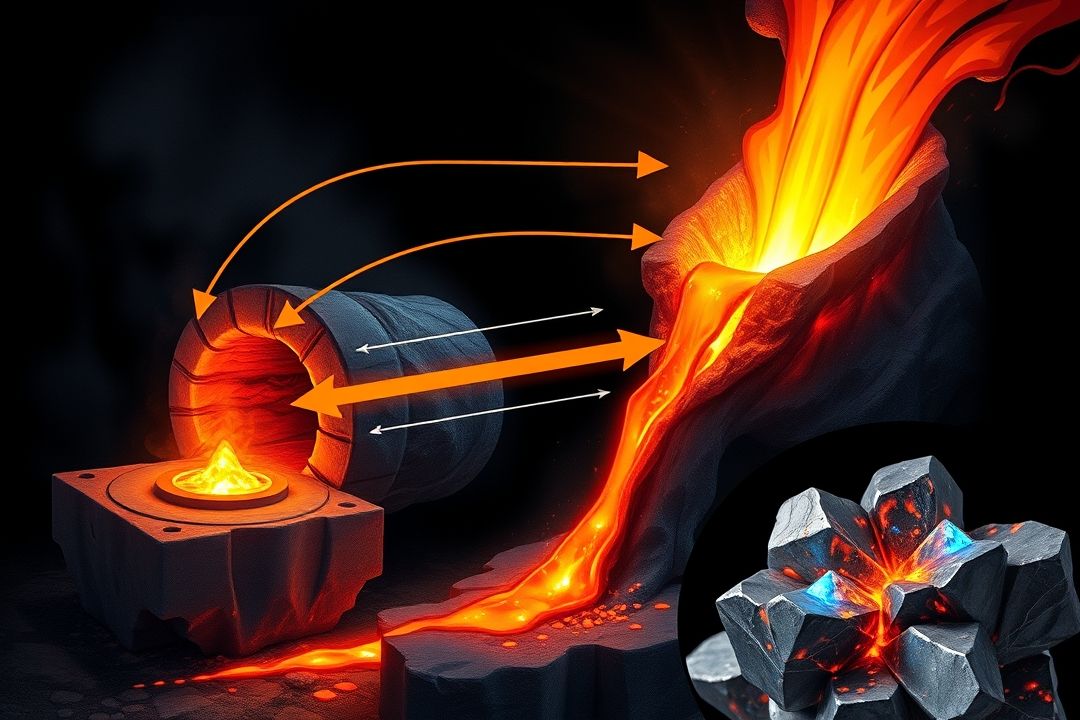
Направленное затвердевание: что это такое и как оно работает
Процесс направленного затвердевания – это важная технология в области литья металлов, которая позволяет получать качественные детали без усадочных дефектов. Этот метод постоянно используется в различных отраслях, таких как автомобилестроение, машиностроение и производство оборудования. В этой статье мы подробно рассмотрим, что же такое направленное затвердевание, как оно осуществляется, его преимущества и отличия от других методов затвердевания.
Суть направленного затвердевания
Направленное затвердевание представляет собой метод, при котором расплавленный металл подается в форму с выдерживанием определенной температуры. Это приводит к тому, что металл начинает остывать и затвердевать по направлению к потоку. Важно, что процесс затвердевания начинается с дальнего конца формы, а затем перемещается к источнику расплава. Благодаря этому методу удается избежать образования полых пятен и усадочных дефектов, которые могут существенно снизить прочностные характеристики готовой детали.
Процесс направленного затвердевания
При направленном затвердевании металл, попадающий в форму, начинает остывать, и затвердевание начинается в тех местах, которые находятся дальше от источника горячего расплава. Этот метод позволяет контролировать скорость подачи расплавленного металла и вносить коррективы в температурный режим формы. Таким образом, жидкий металл имеет возможность сам заполнять возникшие пустоты и провалы.
В процессе направления затвердевания важно следить за температурой не только самого расплава, но и формы, в которую он заливается. При правильном температурном режиме снижается вероятность образования дефектов, которые могут возникать из-за того, что металл остывает неравномерно.
Отличие направленного затвердевания от прогрессивного затвердевания
Необходимо отметить, что направленное затвердевание не следует путать с прогрессивным затвердеванием, также известным как параллельное затвердевание. В последнем случае процесс охлаждения начинается с внешних стенок отливки, тогда как при направленном затвердевании охлаждение начинается снизу, что позволяет более эффективно контролировать заполнение формы и предотвращать образование дефектов.
Параллельное затвердевание может привести к образованию напряжений и дефектов, так как части детали остывают с разной скоростью. Например, в L-образной форме может наблюдаться слишком быстрое охлаждение в углах, что создает узкие места и воздушные карманы, ослабляющие структуру. Поэтому контроль параллельного затвердевания и поощрение направленного затвердевания – важные аспекты процесса литья.
Методы контроля направленного затвердевания
Существует множество методов, позволяющих контролировать процесс направленного затвердевания. Все они направлены на удержание постоянной температуры, чтобы исключить резкие колебания, которые могут повлиять на качество детали. Одним из наиболее распространенных методов является использование терморегуляторов и теплоотводящих элементов, которые помогают поддерживать нужную температуру камеры.
Некоторые производители используют изолированные гильзы, которые обеспечивают стабильную температуру пресс-формы. Эти устройства позволяют избежать перегрева или переохлаждения отдельных участков формы. Еще один важный аспект регулирования – это контроль скорости потока расплавленного металла, его температура и состав. Каждый из этих факторов может существенно повлиять на конечный результат.
Преимущества направленного затвердевания
Процесс направленного затвердевания обладает рядом преимуществ по сравнению с традиционными методами литья. Во-первых, этот метод значительно снижает риск возникновения усадочных дефектов и полостей, что делает готовую продукцию более прочной и долговечной. Во-вторых, он позволяет создавать более сложные формы и конструкции, которые невозможно произвести с использованием традиционных методов литья.
Кроме того, благодаря направленному затвердеванию можно достичь более высокой точности и однородности механических свойств материала. Эти характеристики важны в производстве, где требуется высокая степень надежности и долговечности деталей, таких как в авиационной и автомобильной промышленности.