Превращение жидких пластиковых смол в твердые, пригодные для использования объекты и детали — это современная наука, которая обычно выполняется с использованием литья под давлением машина. Машины бывают разных размеров, размер машины определяется желаемыми размерами готового продукта. Изобретенный в 1872 году процесс литья под давлением произвел революцию в индустрии пластмасс. В настоящее время это многомиллиардный бизнес, который производит около 32% по весу всего пластика в мире. Его популярность объясняется процессом литья под давлением и машинами, на которых производятся миллионы потребительских товаров, а также производством деталей и компонентов, которые доступны по цене, но прочны и долговечны.
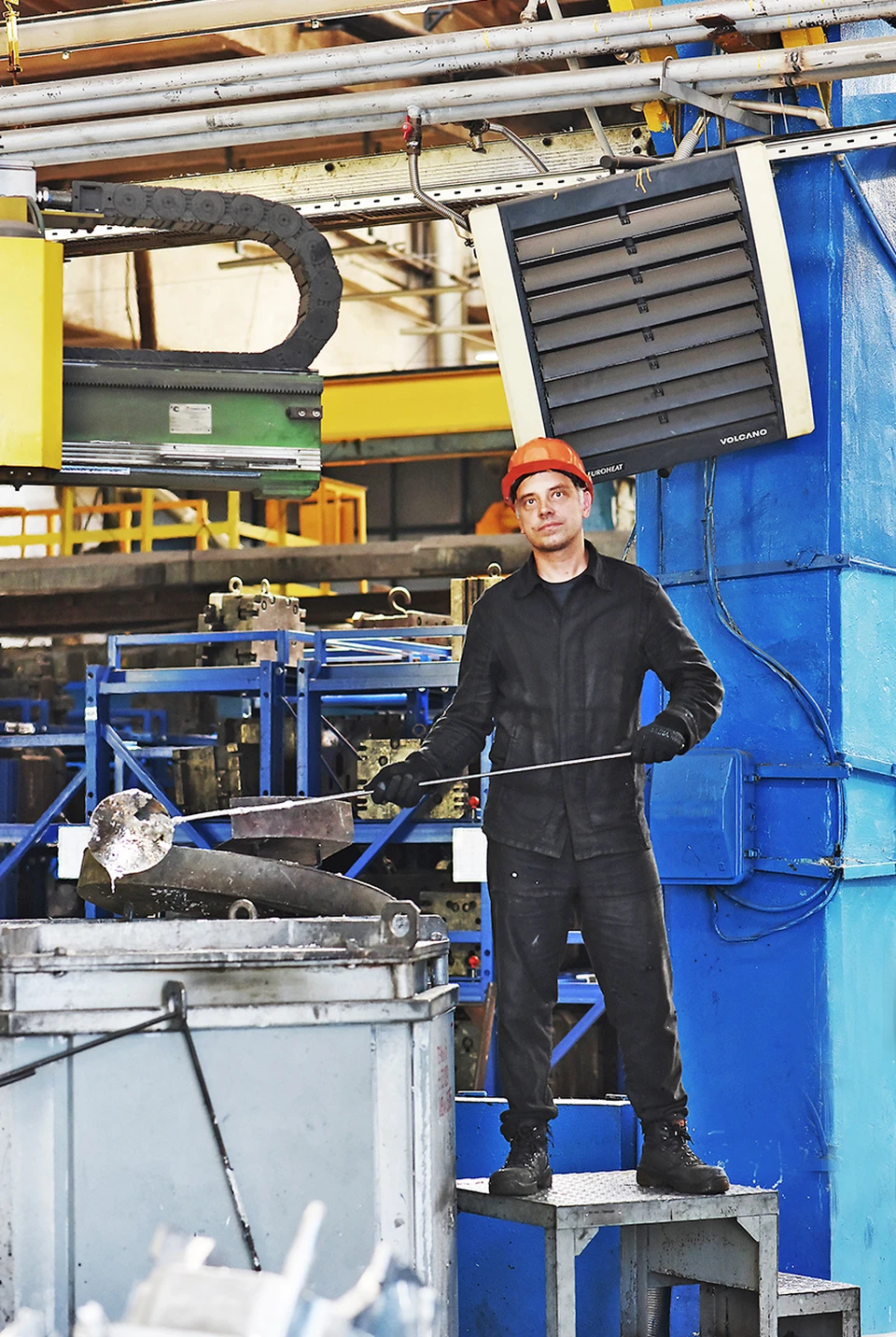
Устройство термопластавтомата и его эксплуатация достаточно просты. Машина состоит из шести основных частей. Основные компоненты машины включают в себя бункер, в который загружается сырье, бочку для подачи материалов к нагревательному блоку, нагреватель для разложения материалов на жидкость, сопло для перекачивания жидкости в форму, узел зажима. для затвердевания формы и эжектор для выталкивания готового продукта.
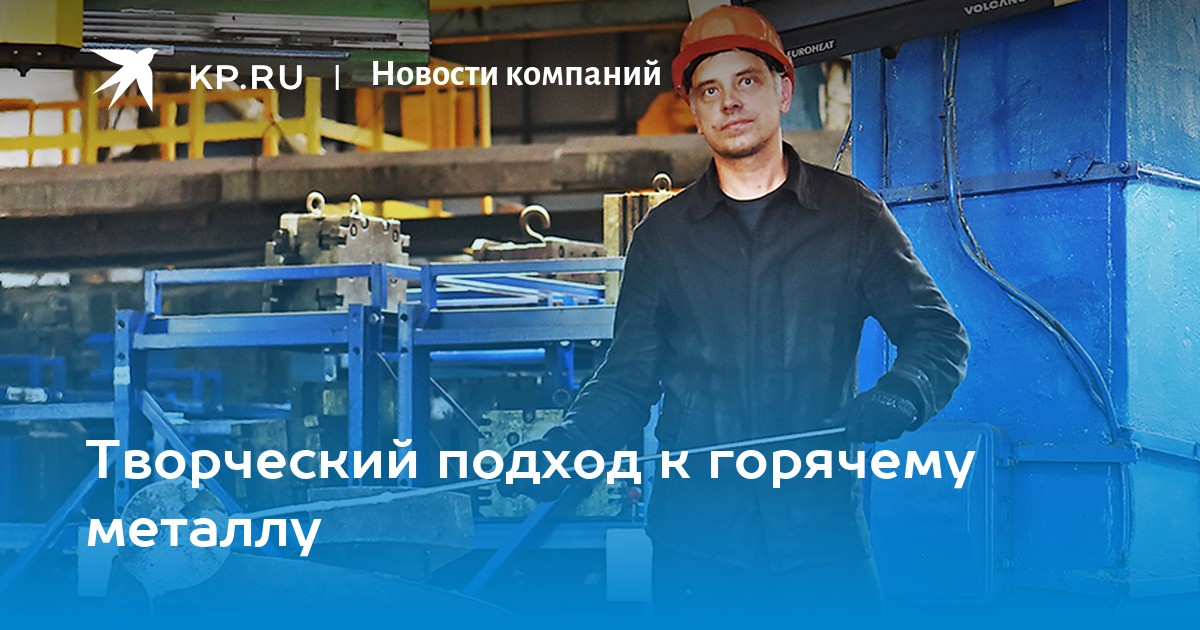
Для производства литьевого изделия в бункер машины для литья под давлением заливают жидкую смолу, а затем красители или красители. Сила тяжести втягивает смолу в бочку, а в процессе нагревания смола превращается в однородную жидкость. Механизм впрыска, обычно возвратно-поступательный шнек или плунжерный инжектор, нагнетает жидкость в форму. Если требуется небольшое количество смолы в форме, используется возвратно-поступательный шнек, поскольку он может впрыскивать всего 5% от всего количества в бункер. Плунжерный инжектор используется, когда не менее 20% от общего количества в бункере необходимо нагнетать в форму.
Форма определяет форму готового продукта и охлаждает жидкость до твердого состояния. В процессе охлаждения пластины пресс-формы удерживаются вместе за счет механической или гидравлической силы. Эта процедура зажима определяет окончательную форму готового изделия. Поскольку разные смолы имеют разные значения усадки, формы разрабатываются с учетом конкретных смол.
Проблемы с производительностью машины для литья под давлением обычно несложны и легко решаются. Сгоревших или опаленных частей можно избежать, снизив температуру бункера или сократив время обработки. Коробление обычно решается путем регулировки температуры поверхности формы или толщины формы. Дефекты поверхности продукта можно исправить, отрегулировав температуру формы, уровень влажности или давление.