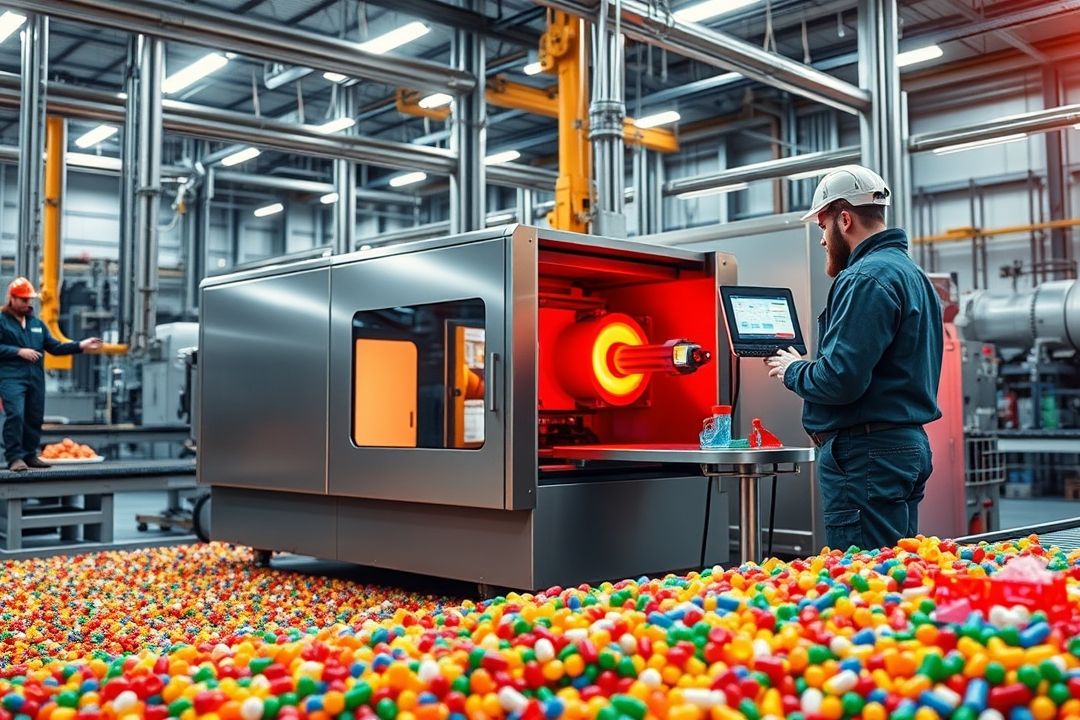
Литье пластмасс под давлением: что это такое и как оно работает
Литье пластмасс под давлением — это один из самых распространенных и экономически эффективных методов производства пластиковых изделий. Этот процесс позволяет создавать широкий ассортимент товаров, от простых предметов быта до сложных компонентов для автомобилей и электроники. В этой статье мы подробно рассмотрим, что такое литье пластмасс под давлением, как оно работает, его преимущества и недостатки, а также его влияние на окружающую среду.
История литья пластмасс под давлением
Процесс литья под давлением был впервые разработан в 1868 году Джоном Уэсли Хаяттом, который использовал целлулоид для производства бильярдных шаров. Он создал первую машину для литья под давлением, которая значительно упростила процесс производства. В 1946 году Джеймс Хендри усовершенствовал эту технологию, разработав новую машину, которая стала основой для современных литьевых машин.
Как работает процесс литья пластмасс под давлением
Литье пластмасс под давлением включает несколько ключевых этапов. Сначала пластиковые гранулы или смолы загружаются в специальный бункер машины. Затем они поступают в нагревательный цилиндр, где под воздействием высокой температуры расплавляются. После этого расплавленный пластик под давлением вводится в форму, которая имеет обратную форму конечного изделия.
Форма может быть изготовлена из различных материалов, таких как сталь, алюминий или бериллий. Выбор материала зависит от требований к прочности, стоимости и долговечности формы. В процессе литья под давлением могут использоваться как плунжерные, так и винтовые машины. Винтовые машины более распространены, так как они обеспечивают более равномерное распределение пластика в форме.
После того как расплавленный пластик заполнил форму, он охлаждается и затвердевает, принимая нужную форму. Затем форма открывается, и готовое изделие выталкивается наружу. Весь процесс занимает всего несколько минут и может выполняться автоматически, что делает его очень эффективным для серийного производства.
Преимущества литья пластмасс под давлением
Одним из главных преимуществ литья пластмасс под давлением является высокая скорость производства. Этот метод позволяет изготавливать большое количество изделий за короткий промежуток времени. Кроме того, литье под давлением обеспечивает высокую точность и однородность продукции, что особенно важно для сложных деталей.
Еще одним преимуществом является возможность использования различных типов пластиковых материалов. В зависимости от требований к конечному продукту можно выбрать подходящий вид пластика, который будет соответствовать необходимым характеристикам, таким как прочность, гибкость или устойчивость к химическим веществам.
Недостатки литья пластмасс под давлением
Несмотря на множество преимуществ, литье пластмасс под давлением имеет и свои недостатки. Одним из них является высокая стоимость первоначальных инвестиций. Изготовление форм для литья может быть дорогим, особенно если требуется высокая точность и сложность конструкции. Это может быть проблемой для малых и средних предприятий, которые не могут позволить себе такие затраты.
Кроме того, процесс литья пластмасс под давлением требует тщательного контроля за качеством, так как любые ошибки на этапе производства могут привести к браку и значительным потерям. Также стоит отметить, что не все виды пластика подходят для литья под давлением, и выбор материала может ограничивать возможности дизайна.